Introduction
JetFlow® Automatic Backwash Filters and Strainers are designed on the base of scanning automatic self-cleaning Filter. When the filter screen can not be regenerated only by back washing with inside suction nozzles, JetFlow® Automatic Backwash Filter adopts the augmented injection back-washing design with a high pressure (H.P. for short) pump to clean the filter screen completely. It is the ideal solution for the challenging service conditions such as high TSS liquid, ultra-fine filtration degree down to 5 μm, sticky debris and particles or low inlet pressure. JetFlow® Automatic Backwash Filter can efficiently remove the suspended solids, sediment and plankton from water or water-like liquid. It keeps efficient self-cleaning performance and continuously work with one single filter. Filtration process is not interrupted during back-flushing. Chemical class design of JetFlow® Automatic Backwash Filter is also available to meet the requirements such as high temperature, high pressure, explosion-proof, zero leakage, etc. JetFlow® Automatic Backwash Filters can meet the most demanding requirements.

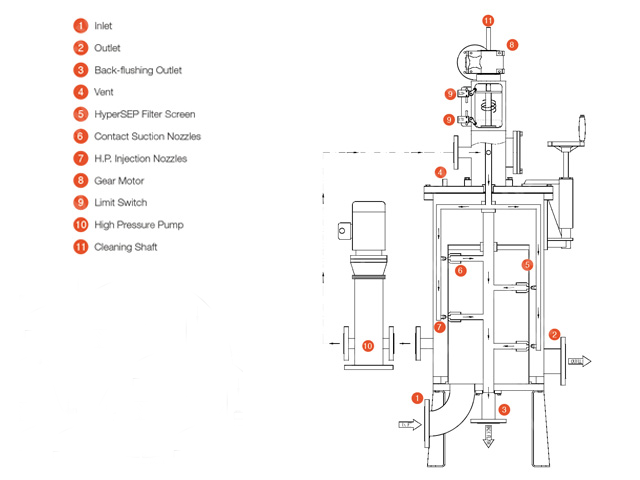
Working Principle
The liquid flows into the screen from the filter inlet, gets through the filter screen and flows out from the outlet. The impurity particles are blocked by the filter screen. After the accumulation of more particles, the filtration pressure drop rises to preset value (normally 50 kPa). Then, the control system triggers the cleaning sequences.
Open the back-flushing valve and start the high pressure pump (up to 1.5~2.0 MPa) . The gear motor drives the cleaning shaft to move helically and reciprocatively at the same time. The inside suction nozzles and outside H.P. injection nozzles are mounted on the same shaft and point at the same area. The shaft rotates helically and drives the nozzles to clean the screen. As the back-flushing valve is open, the differential pressure happens at the position of screen where suction nozzles contact ( The differential pressure = outlet pressure - back-flushing outlet pressure). The outside filtrate flows through the screen into the suction nozzles. Also the H.P. pump takes the filtered liquid and injects the clean liquid to reinforce the back-flushing performance. The impurities and particles on the inner surface are flushed off the screen by the high speed reverse flow and the screen filtration capacity is regenerated. After all of the screen area is scanned and cleaned by the suction and injection nozzles, one self-cleaning cycle is completed. During back-flushing, the filtration process is not interrupted and low flowrate fluctuation and outlet pressure decrease happens.
The JetFlow® Automatic Backwash Filter can run in two modes.
1. All-time suction and injection back-flushing. Every self-cleaning cycle, the suction back-flushing and H.P. injection back-flushing work together.
2. Real-time suction and injection back-flushing. The H.P. injection reinforcing back-flushing steps in when the suction back-flushing interval is shorter than preset.
Specification
Standard Design Pressure | 0.6/1.0MPa (Depend on the Filter Model and Custom-made Requirement) |
---|---|
Mini. Working Pressure | 30 kPa (Even Flowing by Gravity) |
Flowrate Range | 5~1000m³/h(Depends on the filtration degree and ppm) |
Applicable Liquid | Water: Sea Water, Fresh Water, Other Raw Water Processs Liquid: Amine, Methanol, Feed Oil, Fuel |
Back-flushing Liquid | Filtered Clean Water |
Filtration Degree | 3~300μm |
Working Principle | Single Filter Continuous Filtration, Automatic Back-flushing |
Design Temperature | 0-120 ℃ (Standard Type) /0-300℃ (Chemical Class) |
Back-flushing Cycle | Differential Pressure 50kPa and Time |
Differential Pressure Instrument | Intelligent Differential Pressure Transmitter |
Inlet and Outlet Size | DN50~DN350 |
Installation Direction | Vertical |
Inlet and Outlet Standard | DIN Flange PN10 / ANSI Flange CLASS150 |
Housing Wet Part Material | CS/304/316L/Duplex SS 2205/GRP |
Filter Screen Material | 304/316L/904L/2507 |
Internal Parts Material | PTFE、POM、316L/2507 |
Carbon Steel Anticorrosion | Rilsan Coating/ Rubber Lining |
Sealing Material | NBR/EPDM/VITON |
Injection Cleaning Pump | Mult-stage Centrifugal H.P. Pump |
Back-flushing Valve | Pneumatic Butterfly / Ball Valve |
Facility Supply | 380V AC,0.4-0.6MPa Clean and Dry Compressed Air |
Custom-made Design | Explosion Proof Design Involving Instruments and the Control System Designed and Manufactured per ASME / GB150 / PED Pressure Vessel Code Zero-leakage Shaft Sealing Design for flammable, explosive and toxic chemical fluids |